- 1° step
attach the 3D file of the model to be created - 2°step
select the type of shape to be executed - 3° step
select the type of processing based on the timing and quality you want to achieve
3 simple steps: these are the only actions required of the operator
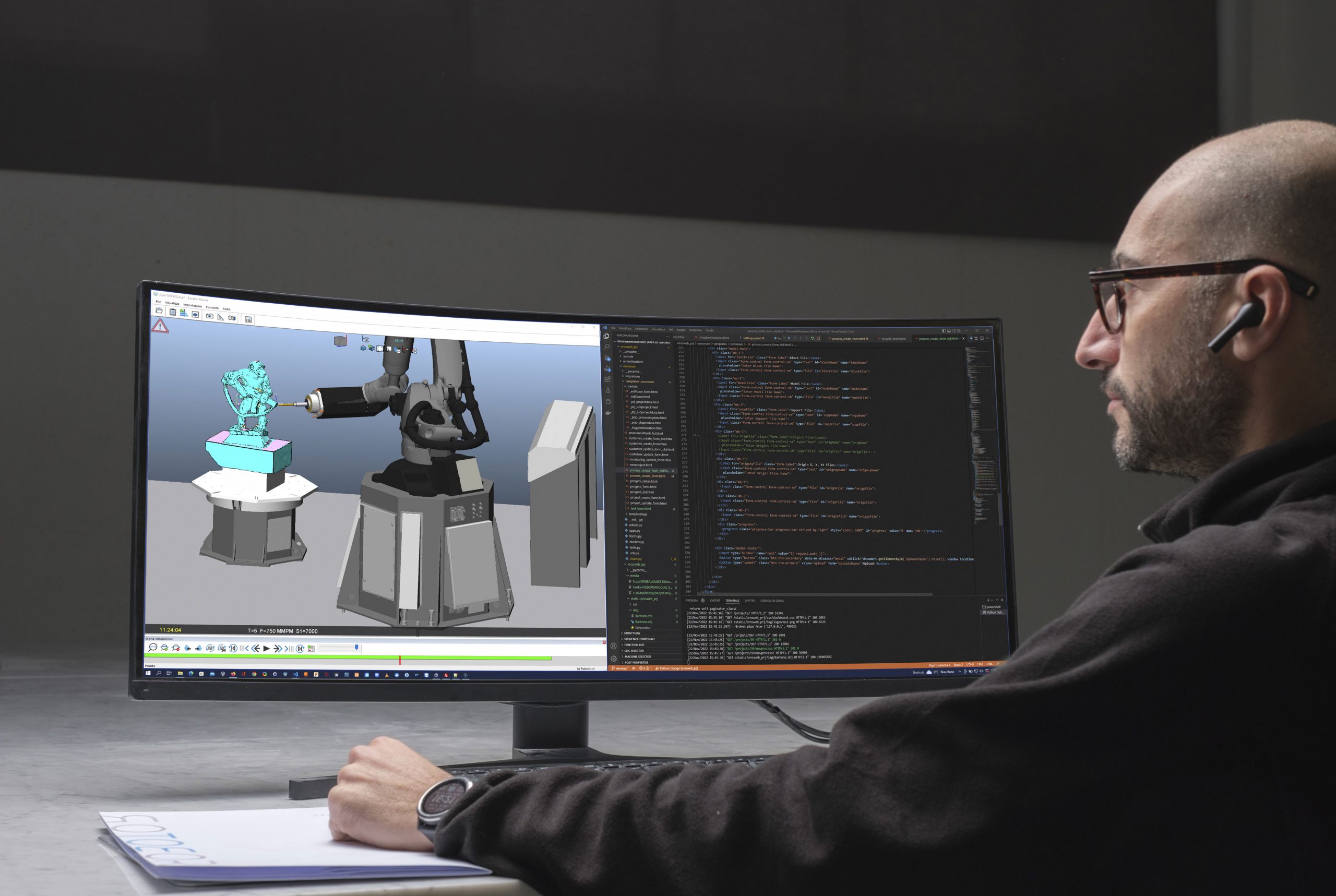
Technological innovations for processing control: 24/7 operability
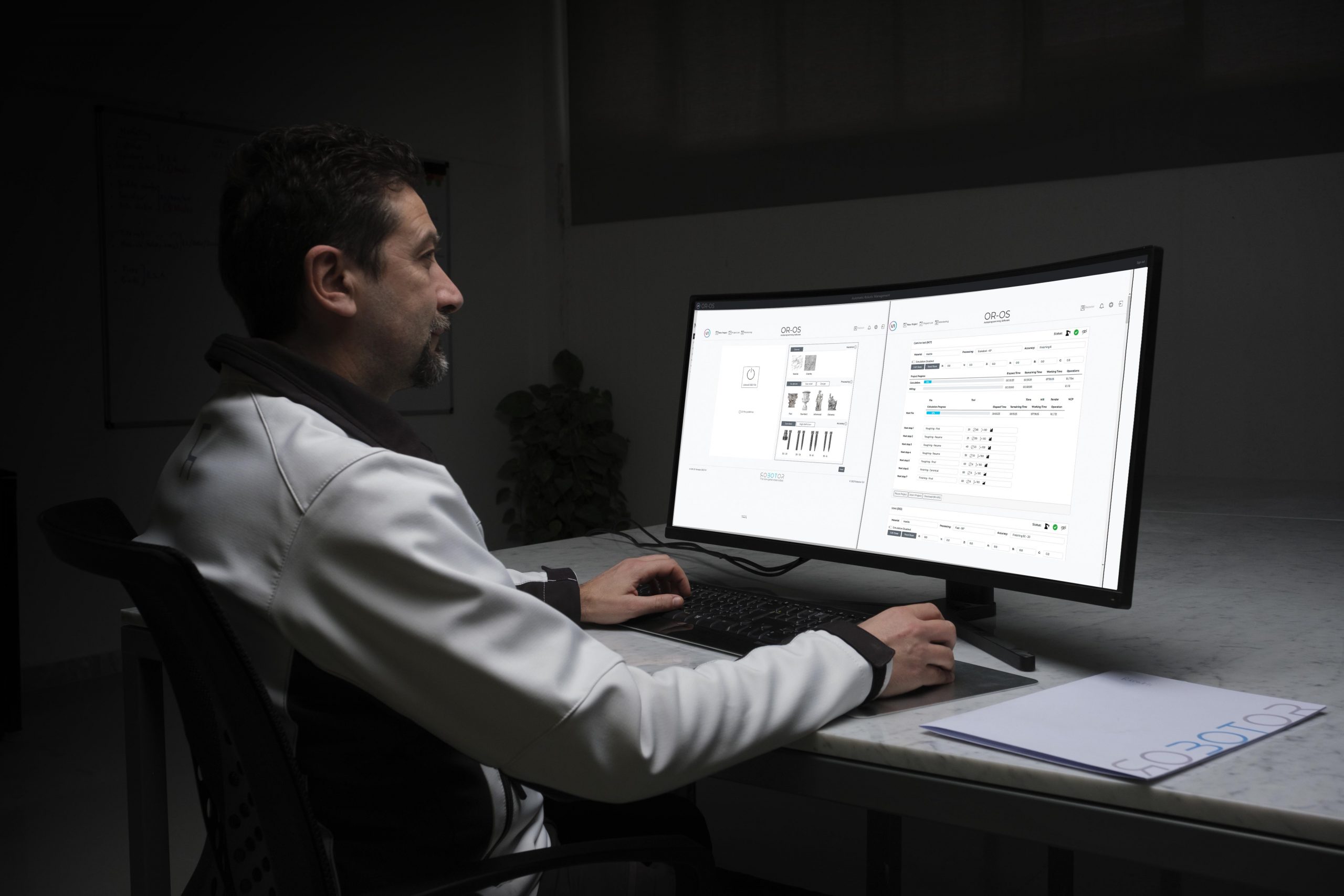
All informations are collected through digital devices.
The obtained datas are sent to dedicated software for the complete verification of the different operational stages.
ROBOTOR’s robots enable uninterrupted operation thanks to adaptive control of processing speed, tool consumption control, and more, all verifiable through the dedicated APP.
OR-INTERFACE Human Machine Interface
OR-OS© communicates with OR-INTERFACE for real-time milling control
Controlled start of the CNC program
Controlled tool change
Adjustment of the robot’s speed and Cyber Spindle
Revolutionary functions: “Adaptive Cruise Control”, “Resume Position”, “Home” selection
and intelligent “Tool list” to calculate paths
OR-SAFE CONTROL Automatic Control Interface
Real-time monitoring of the robot and component status (effort, temperature, vibrations,
etc.) and facilitates intervention in case of anomalies through alerts
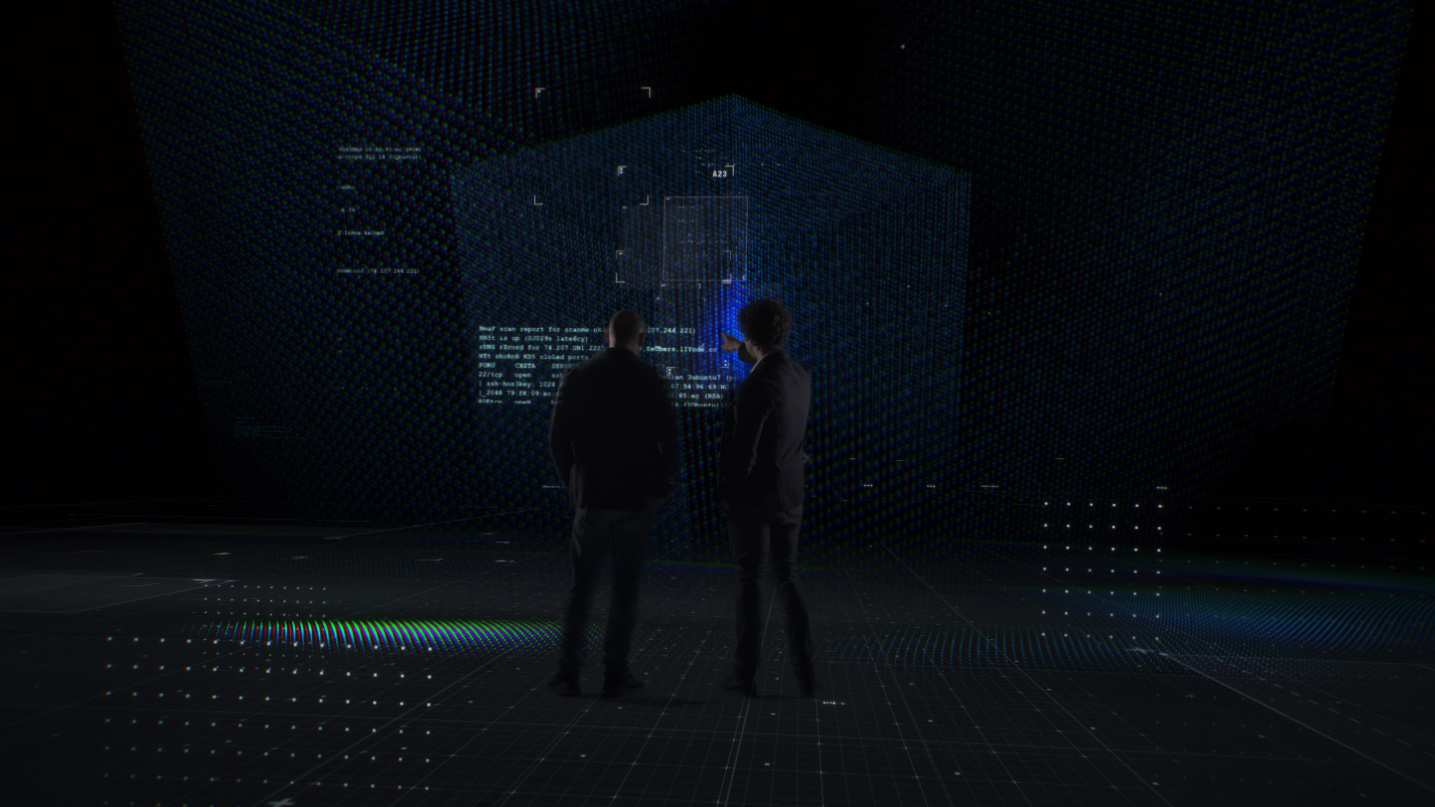
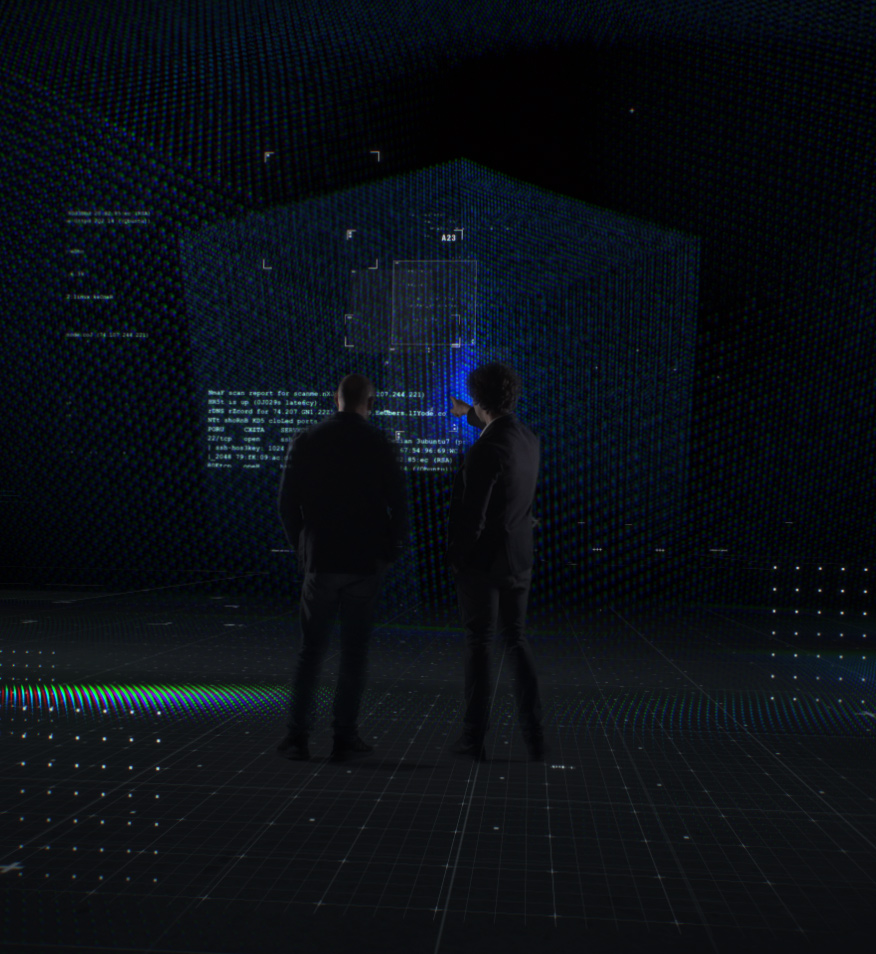
OR-CLB Automatic Robot Calibrator
The TCP (Tool Center Point) calibration phase, essential to start processing, is carried out
completely automatically.
OR-OPCUA Machine Platform Communications
It allows you to remotely manage OR-Safe Control and OR-Interface
OR Interface
CONTROL OF MILLING IN REAL TIME
✓ Controlled start-up of CNC program
✓ Controlled tool change
✓ Speed adjustment of the robot and Cyber Spindle
✓ Revolutionary functions: “Adaptive cruise control”, “Resume Position”, “Home” selection and intelligent “Tool list”
OR Safe Control
MACHINE STATUS CONTROL
✓ Monitors in real time the status of the robot and components (strain, temperature, electronic issues, etc.)
✓ Ease of intervention in case of anomalies, with alerts
✓ Remote support